Fawaz didn’t plan to become a site engineer. At 16, fresh out of secondary school, he took a holiday job in construction to make some money. That one holiday changed everything.
Seven years later, after completing his civil engineering diploma at Yaba College of Technology (YabaTech) and spending every break working in construction, he now supervises full-scale projects in Lagos. In 2024, he worked on a ₦200 million one-storey residential building in Surulere, Lagos.
From unexpected government fines to skyrocketing material costs, here’s the real cost of bringing a house to life in Lagos, brick by brick.
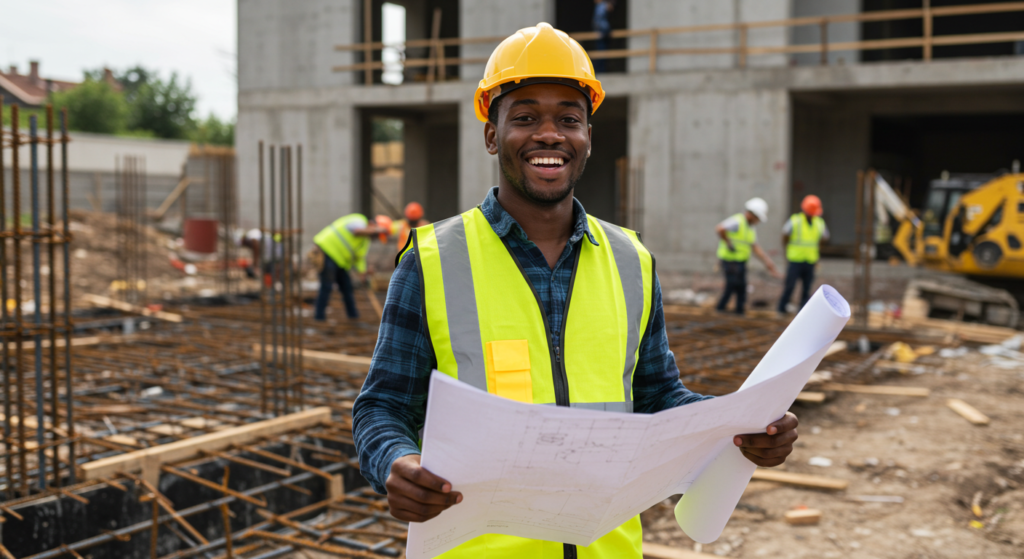
This is Fawaz’s story as told to Aisha Bello:
I’m a junior site engineer in Lagos. This means I supervise the construction of buildings, ensuring everything — from the foundation to the finishing — is done right.
Last year, I helped build a fully finished one-storey residential building in Soloki St, Surulere. The owner contracted the construction firm I work with to oversee everything. We took care of everything from sourcing materials to final fittings. But as with most projects, things didn’t go exactly as planned.
Buying the Land & Paperwork – ₦120.5M
The first step in building a house isn’t construction; it’s paperwork. The owner bought a plot of land for ₦120 million. Before any work started, a lawyer was brought in to verify documents like the Certificate of Occupancy (C of O), Deed of Assignment, and Family Receipt to confirm the land wasn’t being used as collateral for a bank loan. The lawyer’s service alone cost ₦500,000.
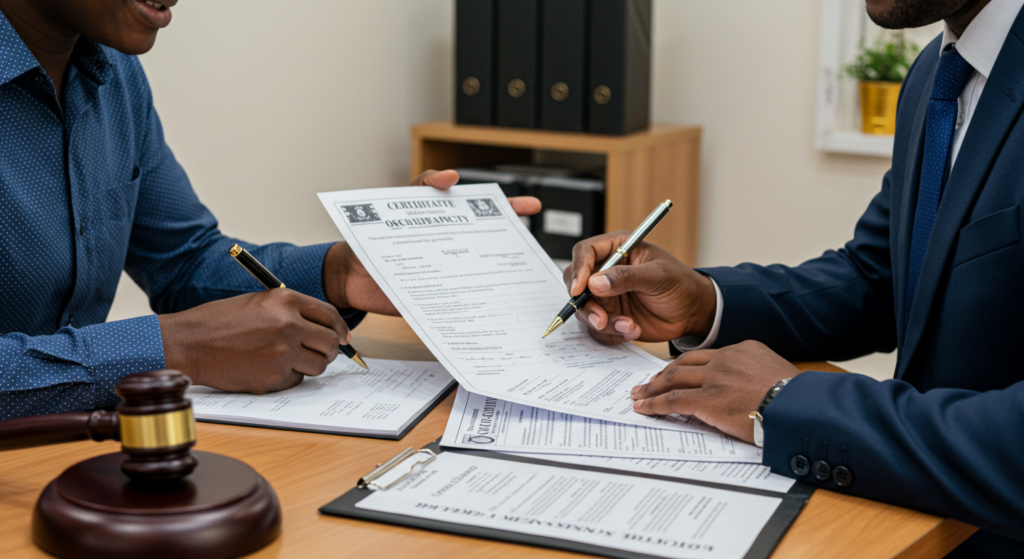
Then, we did a soil test for ₦300,000 to determine the type of foundation the building needed. We drilled deep into the ground, collected soil samples, and tested them in a lab. Based on the results, we went with a raft foundation to prevent future structural issues.
The next step was to get an architect to design the house according to the owner’s vision, which cost ₦700,000. But a design isn’t enough; you also need a structural engineer to ensure the building won’t collapse under its own weight. That’s where the structural drawing came in, which cost ₦300,000.
Once all the plans were ready, my boss, the owner of our construction company, took over. We charged ₦10 million to execute the project from start to finish. This fee covered expertise, project management, and the skilled labour we needed to make the architectural drawings a reality.
Construction Pricing: Why We Charge Per Stage
When people hear the cost of building a house, they assume it’s a fixed number from start to finish.
But that’s not how we work.
While the contractor’s fee is paid upfront (in this case, ₦10 million), the actual money spent on materials and labour is determined stage by stage.
Construction material prices change almost every day in Nigeria. If we estimated the total cost at the beginning and stuck to it, we’d either run into losses or get stuck midway when the prices of materials shot up.
So at every new stage, we confirm current prices and bill the client accordingly. That way, they’re only paying for materials at the actual market rate when they’re needed.
Foundation – ₦10.5M
This was one of the most expensive parts of the project. A building’s strength is in its foundation. You can’t afford to cut corners when laying a foundation; one mistake can collapse the entire building.
Here’s how we laid the foundation:
Step 1: Excavation and Digging
We paid ₦200,000 to dig out the ground for the foundation. This is hard labour: men with shovels and sometimes machines, depending on the land.
Step 2: Laying the foundation
Once we finished digging, we started laying the foundation in the dug-out space called the trenches.
How we laid the foundation:
- Reinforcing the trenches: To strengthen the foundation, we placed 3.5 tons of imported iron rods ( ₦4 million) in the dug trenches.
- Setting up the framework: We used 100 Marine boards (₦2,800,000) to build moulds that held the concrete for the foundation. One marine board went for ₦28,000.
- Mixing and pouring concrete: We combined 375 bags of cement (₦2.8 million), two trucks of granite ( ₦1 million) and two trucks of sharp sand (₦600,000) and spread the mix evenly.
- Installing the German floor: To improve stability, we layered another thick slab of concrete floor to reinforce the foundation.
- Labour cost: We paid labourers ₦400,000 and ₦250,000 to cast the German floor and lay the foundation.
- Total foundation cost: ₦8 million.
It took 40 labourers to get this done.
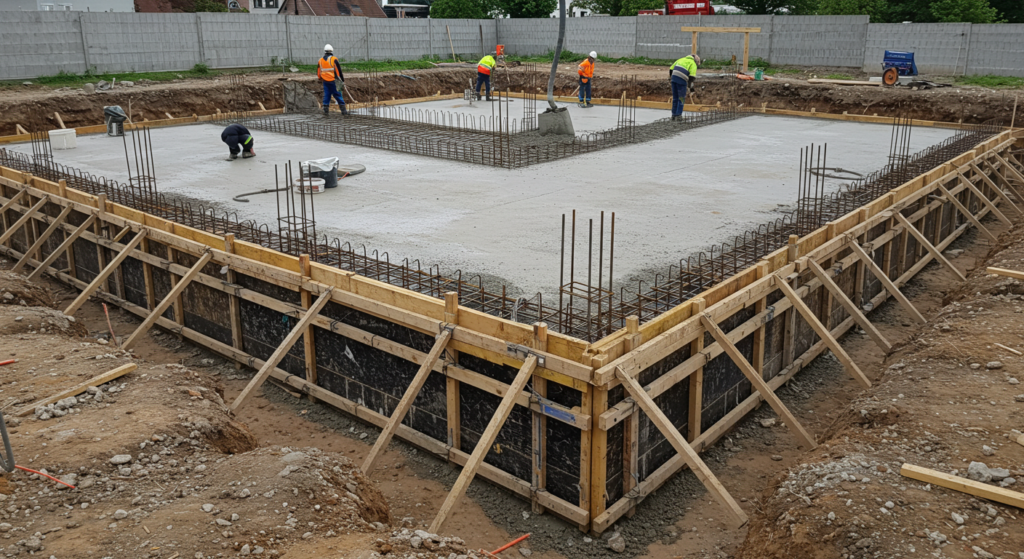
Unexpected Delay – ₦2M Fine
We started the project in September 2023 with a completion timeline of 7–9 months. However, three months in, construction was halted because the owner had lied about getting government approval to build a storey building in the area. The Lagos State Building Agency (LASBA) stopped our work, and it took three months to resolve the issue. We ultimately had to pay a ₦2 million penalty before work could resume in January 2024.
Superstructure (Walls & Decking) – ₦7.5M+
Once the foundation was solid, we started raising the structure. This process is done in stages:
1. Columns (Pillars)
Columns are the skeletal framework of the house — the vertical and horizontal supports that hold everything together. We paid:
- Iron bender (20 pillars): ₦100,000.
- Carpenter: ₦100,000.
- Labour for casting (20 pillars): ₦140,000.
Whenever we cast a structure, we need iron for reinforcement, woodwork for formwork, and concrete to hold everything together.
Once the structure was in place, we moved to the next big stage.
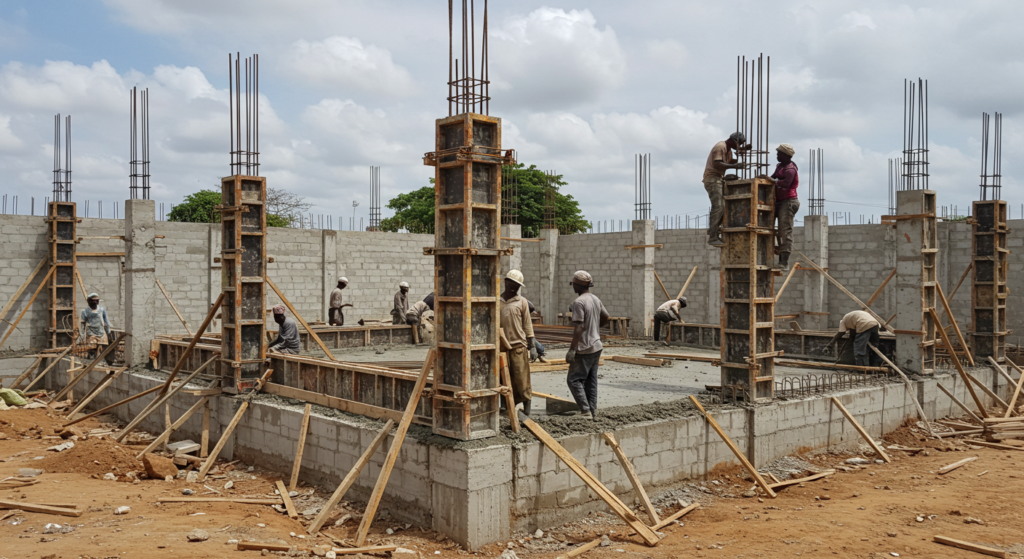
2. Decking: The floor between two storeys
If a building has more than one floor, you need a solid concrete slab between them. This is called the decking slab, and it’s a major part of construction costs.
First, we had to mould hollow blocks, which are cheaper and reduce the amount of granite and sharp sand needed. This required 200 bags of cement and ₦200,000 paid to workers to mould the blocks.
For the actual decking slab, we needed:
- 130 bags of cement (₦7,500 per bag).
- 2 extra tons of iron rods (₦1.9m per ton).
- Workmanship for iron bending and carpentry: ₦250,000 each.
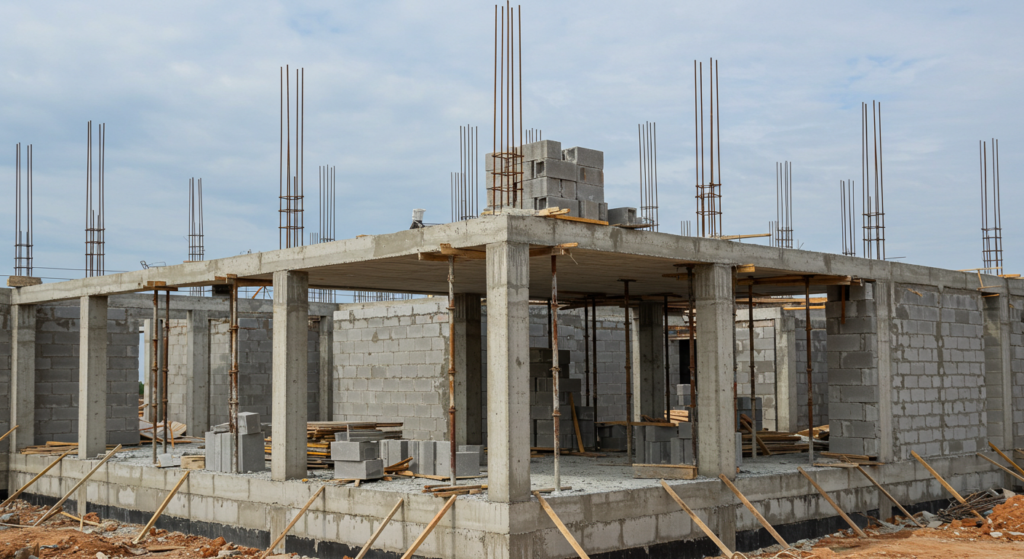
3. Another set of Columns (Pillars)
After the decking, we needed to raise another 20 columns to support the next level. Since fewer materials are needed as you go higher, this stage costs less than the foundation columns.
- Iron bender (20 pillars): ₦50,000.
- Carpenter: ₦85,000.
- Labour for casting (20 pillars): ₦140,000.
4. Roof Beam & Logging
The roof beam is a reinforced concrete frame that keeps the building stable and distributes the roof’s weight evenly.
- We cast the roof beam using leftover concrete from the decking.
- Planks and iron rods were used to reinforce the edges.
Next, we worked on roof logging, which is the wooden framework that supports the roofing sheets. This involved securing planks before adding a small slab for the water tank.
At this stage, the house’s skeleton structure was complete. Now, it was time for the walls.
5. Walls
For the walls, we needed about 3,000 blocks.
- 9-inch blocks (2,300 pieces @ ₦730 each): ₦1.68M.
- 6-inch blocks (700 pieces @ ₦630 each): ₦441,000.
- Labour for lifting 3,000 blocks to the first floor: ₦75,000 (₦25 per block).
- Labour for laying blocks: ₦280,000.
- Extra materials (cement, sharp sand, granite): ₦1.5M.
Roofing – ₦15M
Roofing is one of the most expensive aspects of building in Lagos, especially if you’re using the costly but durable aluminium sheets.
- Aluminium roofing sheets: ₦8 million.
- Woodwork & roofing labour: ₦7 million.
Internal Work – ₦63M+
Once the structure is complete, we move indoors for the finishing touches. This is where things really add up, and the house starts looking like a home.
- Plumbing: ₦12 million (materials) + ₦2 million (workmanship).
- Tiling: ₦9 million (materials) + ₦2.5 million (workmanship).
- Electrical work: ₦7 million (materials) + ₦2 million (workmanship).
- Aluminium work, rails and windows: ₦15.5 million (materials) + ₦3.5 million (workmanship).
- Wall plastering: ₦1.4 million (sand) + ₦400,000 (labour) + 400 bags of cement.
- Painting & Screeding: ₦5 million (materials) + ₦2 million (workmanship).
- POP Ceiling: ₦10,200 per bag of POP cement × 180 bags + ₦450,000 (workmanship).

Final Touches – ₦15M+
This is the final stretch: fencing, gate, and finishing touches. Neighbouring buildings already provided two walls for the fence, so we only needed to fence the front and back.
Fence & gate:
i. 150 blocks + 300 bags of cement: ₦2.4 million.
ii. Gate cost: ₦1.5 million.
Iii. Labour (fencing, gate casting, flooring): ₦350,000.
We cleaned the site, installed doors (₦12 million total), handled final electrical fittings, and completed the interior design (₦250,000).
After all this, a painter touched up the dents and made the house move-in ready. Finally, we handed over the keys.
Total Estimated Cost
- Land: ₦120 million.
- Construction & Labour: ₦121.14 million.
- Total Cost: ₦241.14 million.
Lessons from This Project
One of the biggest lessons I learned is to double-check approvals to avoid delaying projects and having issues with the Lagos State Building Agency.
Today, I’m supervising a shopping mall project in Yaba and another one-storey building in Lawanson, Surulere. My job challenges me to solve problems, lead a team, and bring buildings to life. I enjoy the process so much.
Someday, I hope to own my own construction firm and build homes people will live in for years.
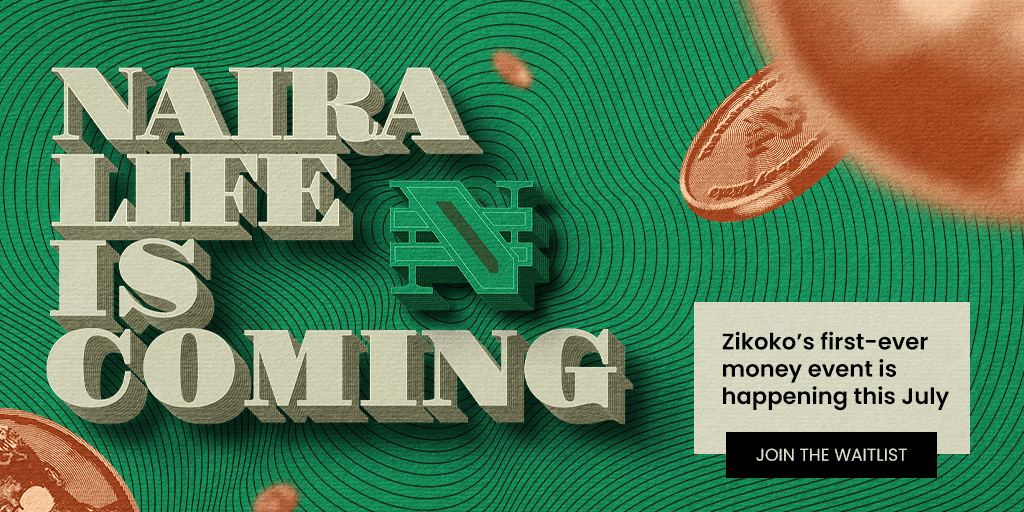
Click here to join the waitlist for Zikoko’s first-ever money event!